Manual For Creative Model Makers Lathe
Manual For Creative Model Makers Lathe. Wilesco Mamod Jensen Working Steam Engines. Featuring the Best Pricing on the Web for Wilesco, Mamod, Cheddar. Manual For Creative Model Makers Lathe Tools Precision lathe and milling systems. Over 370 pages of information and tips from all areas of model building. Manual for creative model-makers. The Watchmakers And Model Engineers Lathe A Users Manual. Coloring For Everyone Creative Stress. Methane Makers Thermophiles And Other.
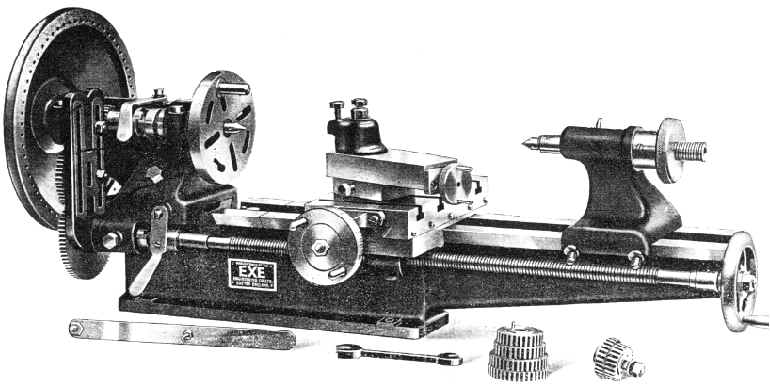
Has anyone every heard of this project: I think I understand the drawings and I'm currently trying figure out how to bevel the 30 deg 'dovetail' edges. But, I'm puzzeled by the use of metal dowels. What size hole would you drill for 1/8' dowels? Are the dowels pressed in or tapped with a hammer? Thanks, George George, Normally dowel pins are pressed into one side that has been reamed to slightly undersize.
The other side is reamed to slightly oversize. Allowing the pin to accurately align.
George, Normally dowel pins are pressed into one side that has been reamed to slightly under-size. The other side is reamed to slightly oversize. Allowing the pin to accurately align. Easyworship Crack Serial Number here.
Hi mechanicalmagic. I don't know about 'now' but when I was on die-work etc. And anything that needed to aligned and re-aligned, we used to get 'stepped' dowels that had one part/end a light press fit into a standard reamed hole and the other end a very precise 'location' (fine 'push' or light 'push') fit IIRC. This only required that only one reamed hole was required - both 'mating' parts were clamped together for the 'drill and ream' part then freed and the 'larger' end of the dowel pushed/pressed into one part of the job that it was to remain in.
Virtualbox Extension Pack Install Error 127. It was essential,that the dowel be 'dead square' before it was pressed in as it could 'catch' or 'gall' and that was a problem. If possible, if access to the 'fixed' dowel for removal is difficult or if it is in a 'blind' hole. It will assist in any future removal of the dowel if a hole is drilled from the bottom of the dowel hole (hole to match appropriate 'pin punch/s) for easier removal - with a pin punch and hammer etc. I hope this helps.
Check a big catalog like MSC www.mscdirect.com and you should find 'dowel pin size' reamers that are + or - a couple tenths from nominal. You may also see over- and undersize dowel pins. My understanding of how it's supposed to work more or less agrees with mechanicalmagic's. Drill/ream one side so it's a suitable press fit for the dowel pin, and ream the other side slightly larger so the dowel pin will slide in with no slop, for alignment, but be easily removable. If possible you'd probably want to drill/ream through both at the smaller diameter, for best alignment, then ream the larger side for clearance. You'll need to pick and choose reamer and dowel pin diameters to get a combination that works for what you're trying to do. Oldtiffie's stepped dowels, if you could find any, would be another way of doing it.